How are polycarbonate hollow sheets made?
Sunlight board, also known as polycarbonate hollow sheets or polycarbonate mutil-wall sheet. it is composed of two or more single-layer boards stacked in parallel and connected by stiffeners. This structure determines that the production of hollow panels requires the use of an extruder to continuously pass the heated raw materials (polycarbonate) through the mold to extrude the plates with the required cross-section shape. it is commonly known as “extrusion method”. Although the principle of extrusion is simple, there are many production steps. Only after fully understanding, can we select plates that meet our own requirements and quality.
Raw material drying
Polycarbonate is a kind of resin that is easy to absorb water, which will affect the physical properties of the board. There are two common drying methods: particle drying and extrusion exhaust.
Add raw materials
Attention should be paid to maintaining stability to avoid layering of different raw materials. Color masterbatch needs to be added for the production of colored solar panels, and the color can be customized according to requirements.
Extrusion filtration
A high temperature of nearly 300 ℃ is required, and the temperature is increased in stages to ensure stability. Filter non-plasticized solid particles to avoid defects such as “black spots” and “cold scars” on the plate.
Sheet forming
The molten material enters the mold after being extruded by the screw and stabilized. The mold is usually made of nickel-chromium-molybdenum steel, and its shape is the shape of the plate to be formed. The sheet forming process is completed after the molten material passes through the mold.
Plate sizing
The key to ensure the smooth and clean surface of the solar panel is to cool the formed panel and finish the initial setting and keep the setting device clean. Pull out the initially shaped plate with the traction roller, and finally shape the plate after annealing to eliminate the internal stress.
Cover with protective layer
The protective layer mainly includes anti-ultraviolet layer and anti-fog layer. The anti-ultraviolet layer is formed by co-extrusion of masterbatch containing ultraviolet absorber and solar panel material. The antifogging layer can be directly applied to the surface of the plate.
Laminated cutting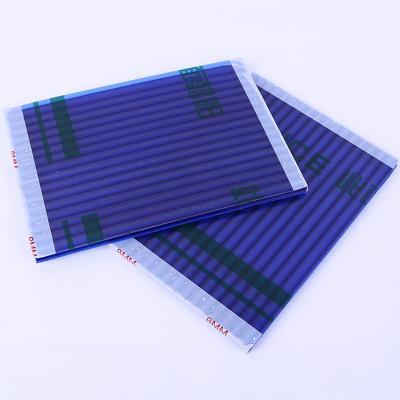
The sun plate has poor wear resistance. After the extrusion molding is completed, it is necessary to apply protective film to the plate and print relevant product information on the plate to prevent scratching. Cut the plate to the required length as required.
Closed packaging
After cutting the plate, immediately seal the cutting section with self-adhesive tape, so as to avoid contamination of the plate cavity. After being packed with corrugated cardboard and white low-density polyethylene film in turn, the sunlight board can leave the factory.
Therefore, it is not difficult to see that the extrusion method can produce continuous shape plates along the extrusion direction, and then cut according to the actual length to get the final product. The section form of the solar panel is different due to the difference of the selected extrusion die. The color of the plate is determined by the different color masterbatches added in the raw material. The anti-ultraviolet, self-cleaning, anti-fog and other characteristics of the product are obtained by attaching the corresponding coating to the surface of the plate.
Therefore, some characteristics of solar panels can be controlled by changing processing procedures or production conditions, and the final performance of panels can be deeply customized according to the actual needs of users.
https://www.facebook.com/Amas.awnin
Amas 100*120CM Outdoor Front Door Window Awning Patio Eaves Canopy PC Cover UV AMS-Y100120